Nous vous expliquons comment appliquer la méthode 5S sur le lieu de travail.
Optimiser votre lieu de travail grâce à la méthode 5S ? C’est possible !
Vous arrive-t-il parfois de regretter de ne pas avoir rangé tel ou tel objet au bon endroit ? Ce genre de réflexion indique clairement que le fonctionnement de votre entreprise n’est pas optimal. Vous pouvez perdre un temps précieux à chercher l’équipement dont vous avez besoin, et cette situation induit souvent une baisse de productivité. Pourquoi perdre du temps s’il est possible de procéder autrement ? Découvrez ici comment améliorer le fonctionnement de votre entreprise avec la méthode 5S !
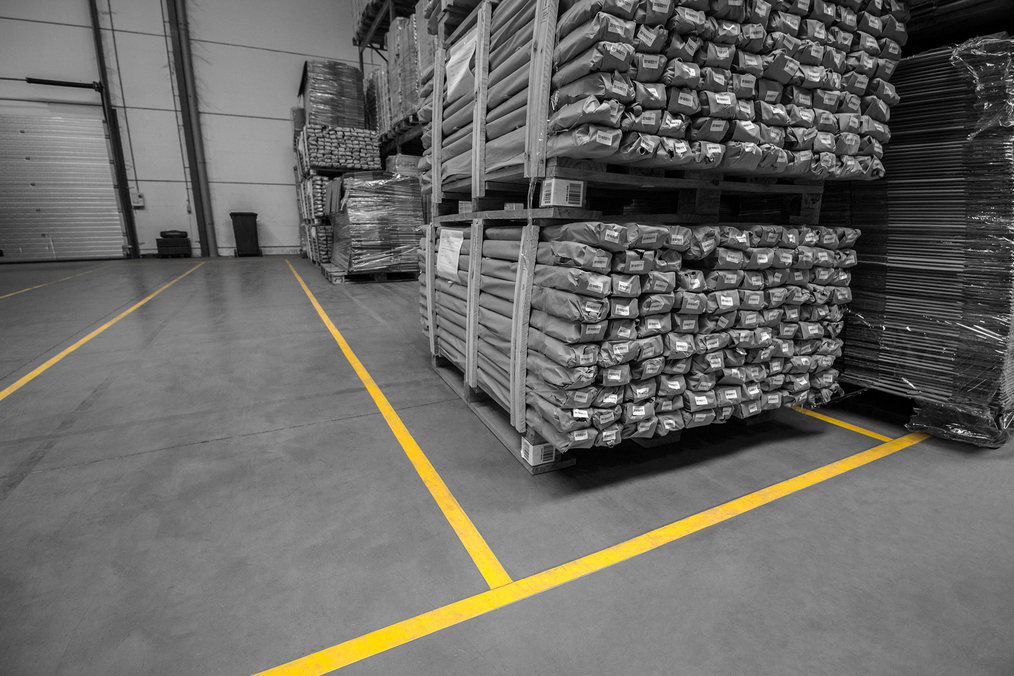
QUE SIGNIFIENT LES 5 S ?
La méthode 5S permet d’optimiser en permanence le fonctionnement de votre entreprise. En respectant les cinq piliers, vos collaborateurs sont en mesure de maintenir ordre et propreté sur leur lieu de travail. La méthode 5S garantit ainsi un meilleur fonctionnement de votre entreprise. Ce qui contribue à améliorer la concentration et la sécurité. La « sécurité » pourrait d’ailleurs être le sixième S...
La méthode 5S a vu le jour au Japon, où elle a été introduite dans les ateliers de production des usines Toyota. L’objectif était de rationaliser les processus de l’entreprise, et donc de gagner en productivité. Dans la pratique, il s’agissait de s’appuyer sur les cinq piliers suivants de la méthode 5S :
S1 : supprimer l’inutile ou SEIRI
Seiri signifie que vous conservez uniquement ce dont vous avez besoin. Nous avons tendance à garder trop de choses. Cette manie de collecter les objets a un impact important sur l’ordre et la propreté au travail. Pour créer de l’espace, ne conservez que ce qui est utile vos activités : il vous faut faire un tri. Jetez les objets cassés ou endommagés, ainsi que ceux que vous n’utilisez plus depuis longtemps ou qui doivent être remplacés. Cela semble évident, mais trop de postes de travail sont encombrés de ces objets « polluants ». Qui de surcroît augmentent le risque de chute, de trébuchement, de heurt ou de glissade.
Commencez donc par supprimer les objets qui ne sont pas nécessaires dans votre espace de travail.
S2 : situer les choses ou SEITON
L’étape « seiton » est résumée par la devise la suivante : « une place pour chaque chose et chaque chose à sa place ». Il s’agit maintenant de ranger ou de stocker tous les équipements ou marchandises au bon endroit. Un stockage optimal vous évitera de perdre du temps et de devoir interroger vos collègues pour retrouver un objet. De plus, une meilleure gestion visuelle permet de mieux organiser l’espace de travail et d’améliorer la productivité. Comment faire ? La réponse est simple. Commencez par définir un emplacement fixe pour chacun de vos outils. Des marquages au sol vous seront également d’une grande utilité. Ce moyen de prévention permet d’éviter que les travailleurs stockent des marchandises au petit bonheur au beau milieu d’un entrepôt. Vous trouverez un marquage au sol adapté à toutes sortes d’applications : des marquages de lignes destinés à délimiter certaines zones au marquage au sol avec revêtement antidérapant, en passant par de nombreuses formes de marquage.
S3 : (faire) scintiller ou SEISO
Maintenant que votre environnement de travail a été débarrassé des objets superflus (SEIRI) et que les marchandises que vous avez conservées sont rangées de manière ordonnée et claire (SEITON), il est temps de passer à la troisième étape : SEISO ou nettoyer votre lieu de travail. Un lieu de travail propre ne vous aide pas seulement à vous y sentir mieux. Il met également au jour d’éventuels problèmes. Imaginez que suite à un problème technique, une machine perde de l’huile. Vous remarquerez immédiatement que quelque chose ne va pas si cette machine est propre en temps normal. Si ce n’est pas le cas, vous risquez de constater le problème trop tard, ce qui peut avoir des conséquences dramatiques telles que des interruptions de travail. Ce n’est pas pour rien que le nettoyage fait partie intégrante de la check-list lors de l’inspection. Il contribue ainsi au maintien d’un lieu de travail sûr.
Par conséquent, établir des règles et des normes pour le nettoyage vous permettra d’éviter l’usure prématurée de vos machines.
S4 : standardiser ou SEIKETSU
Il convient à présent de garder votre espace de travail en ordre. Définissez des procédures, des calendriers et des règles, et respectez-les. Vous obtiendrez ainsi une cohérence dans l’exécution des points d’action susmentionnés. La standardisation (SEIKETSU) permet d’établir une routine qui limite les surprises au maximum.
Ici aussi, le marquage au sol viendra bien à propos, car il rappelle en permanence à votre personnel les règles de sécurité fixées.
S5 : suivre et progresser ou SHITSUKE
Pour tirer profit à long terme des quatre premiers S, il est important de persévérer dans la voie empruntée. L’objectif est ici de créer un climat ou une culture de la sécurité sur le lieu de travail. Vérifiez que tout le monde respecte l’ensemble des mesures préventives et intervenez si ce n’est pas le cas. Une check-list ou des audits sont fortement recommandés pour y parvenir.
Pourquoi pas 5S + 3 ?
Il va de soi que suivre la méthode 5S contribue à la sécurité sur le lieu de travail, ce qui est l’objectif de Boplan ! Les mesures préventives qui favorisent l’ordre et la propreté sur le lieu de travail aident à prévenir les accidents ou les dommages à l’infrastructure. C’est pourquoi nous aimerions ajouter un sixième S à la méthode 5S initiale : la sécurité. La sûreté et la satisfaction peuvent également être ajoutées à l’équation. Ces trois piliers vont plus loin que les mesures purement préventives : les protections de sécurité collective sont également importantes. C’est là la seule manière de vous protéger contre les accidents et les dommages dus aux impacts inévitables.
En fonction du problème de sécurité qui vous occupe et de la situation au sein de votre entreprise, vous pouvez choisir entre différentes applications de sécurité : des barrières de circulation aux protections antichutes, en passant par les solutions antidérapantes.
Chez Boplan, nous vous proposons la solution de sécurité la plus adaptée à vos besoins. Contactez-nous pour en savoir plus sur les applications de sécurité adaptées à votre environnement de travail.
Quels sont les avantages de la méthode 5S ?
Chaque méthode ou règle présente des avantages et des inconvénients. Pour que la méthode 5S fonctionne de manière optimale, la collaboration de tous est nécessaire. Un travailleur qui ne range pas les marchandises au bon endroit influe sur le travail de ses collègues et complique le fonctionnement de l’entreprise. Vos collaborateurs doivent tous suivre les règles de manière méthodique, ce qui n’est pas toujours évident.
La pratique permet de se perfectionner, et offre dans le cas présent de nombreux avantages :
- La méthode 5S est facile à mettre en œuvre et améliore les conditions de travail.
- La méthode 5S renforce la cohésion et l’esprit d’équipe.
- La méthode 5S permet d’avoir un espace de travail ordonné et d’éviter les matériaux qui traînent. Elle contribue ainsi à prévenir les trébuchements et les chutes. Elle constitue donc une étape importante en matière de prévention pour augmenter la sécurité sur le lieu de travail, ce qui améliore à son tour à l’image de marque de l’entreprise.
- La méthode 5S offre aux travailleurs une vision claire de la situation. Ainsi, l’identification des zones avec un marquage au sol contribue à un espace de travail ordonné et à une meilleure localisation des marchandises ou des équipements. Ce qui permet également à vos collaborateurs de gagner du temps.
- La méthode 5S contribue à la productivité, et donc indirectement à l’augmentation de votre chiffre d’affaires.
Comment appliquer la méthode 5S ?
Maintenant que vous savez ce qu’est la méthode 5S, il est temps de l’appliquer. Pour optimiser le fonctionnement de votre entreprise, il est important de procéder étape par étape. Adopter une approche méthodique vous permettra de cartographier chaque espace de votre site et de déterminer s’il répond à chaque S. De cette manière, vous travaillerez progressivement et vous n’oublierez rien. Posez-vous les questions suivantes :
- À quelle fréquence dois-je utiliser cet outil ou cet équipement ? Dois-je vraiment l’avoir en plusieurs exemplaires ? Vous avez répondu à ces questions par la négative ? Retirez l’objet en question de votre espace de travail pour éviter qu’il traîne. (Supprimer – SEIRI)
- Les objets sont-ils au bon endroit ? Puis-je les retrouver facilement ? Vous avez répondu à ces questions par la négative ? Examinez les possibilités de leur attribuer une place fixe. De cette manière, tous les trouveront plus facilement. (Situer les choses – SEITON)
- Faites-vous entretenir régulièrement vos machines ? Vous avez ainsi une meilleure idée de l’état de vos machines et vous pouvez intervenir plus rapidement en cas de problème technique. (Faire scintiller – SEISO)
- Vous remarquez que les règles semblent plus confuses et que vos collaborateurs reprennent leurs anciennes habitudes ? Dans ce cas, vos règles manquent de clarté ou ne sont pas assez suivies. Veillez à les standardiser et à les rappeler sur le terrain. Pour cela, vous pouvez avoir recours à des marquages au sol ou à des produits de sécurité destinés à augmenter la visibilité. Les procédures et les calendriers sont également utiles. (Standardisation – SEIKETSU)
- Un audit régulier vous permet de maintenir l’ordre dans votre atelier. (Suivre et progresser – SHITSUKE)
Vous voulez aller plus loin et miser sur la protection en plus des mesures de prévention ? Informez-vous sur les solutions de sécurité disponibles pour votre atelier. Contactez-nous sans engagement ou consultez notre catalogue. Vous y trouverez des informations et des sources d’inspiration.